Polishing processing for advanced ceramics
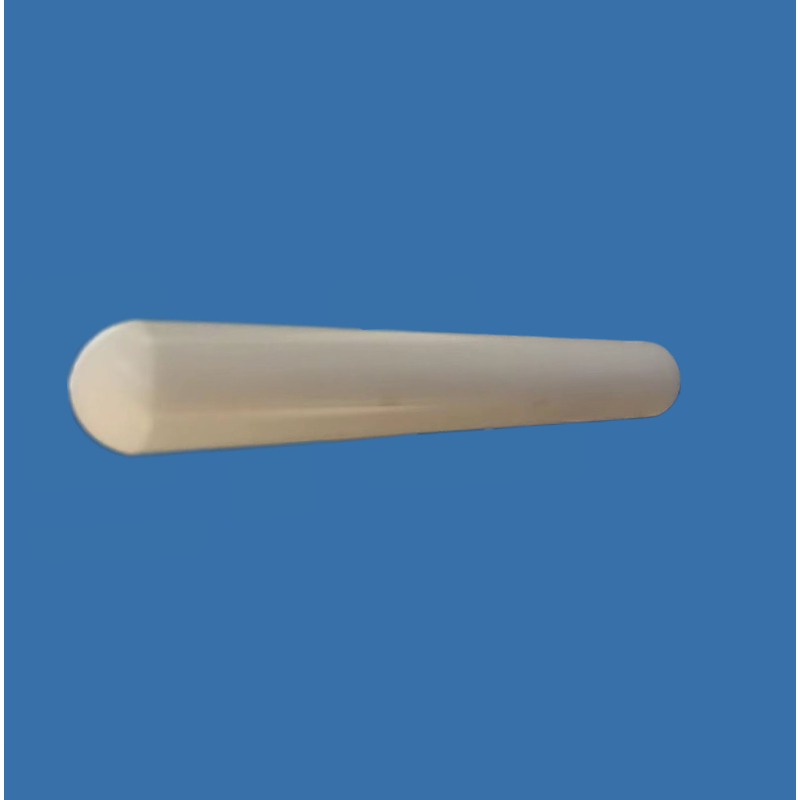
Polishing processing usually refers to the use of mechanical and chemical effects of fine abrasive grains, with the assistance of soft polishing tools or chemical processing fluids, electric/magnetic fields, etc., in order to obtain a smooth or ultra-smooth surface to reduce or completely eliminate the processing deterioration layer, So as to obtain a high surface quality processing method.
Multiple sintering for advanced ceramics

he correct sintering method is the key to make advanced ceramics have ideal structure and predetermined properties. Such as sintering under normal atmospheric conditions (no special atmosphere, normal pressure), no matter how you choose the sintering conditions, it is difficult to obtain pore-free or high-strength ceramic products
Injection molding for advanced ceramics
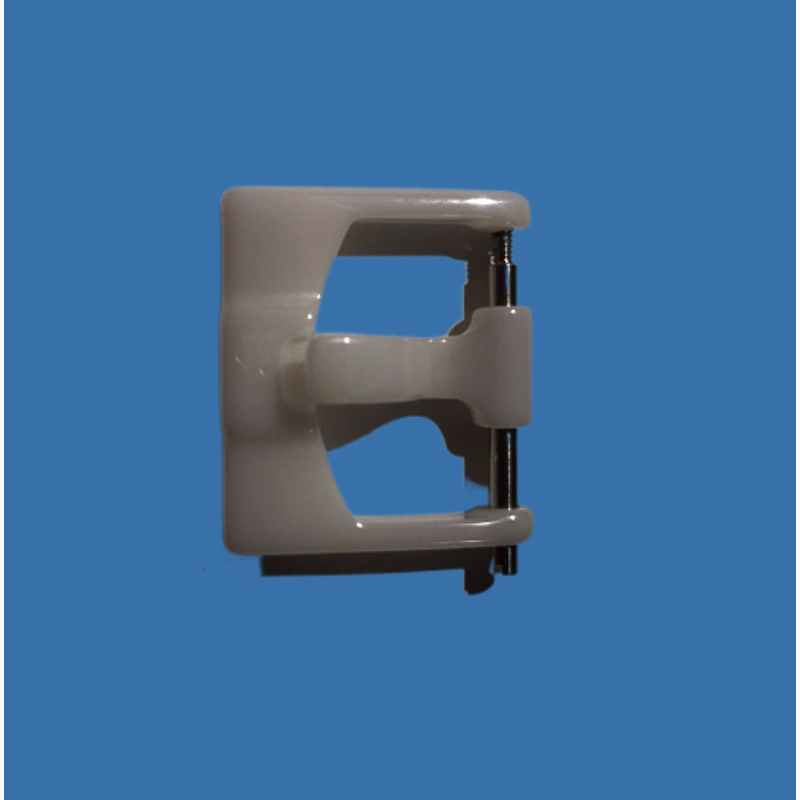
Injection molding is to mix ceramic powder and an organic binder, and then inject the ceramic powder into the metal mold cavity at a temperature of 130~300°C through an injection molding machine.
Isostatic pressing for advanced ceramics
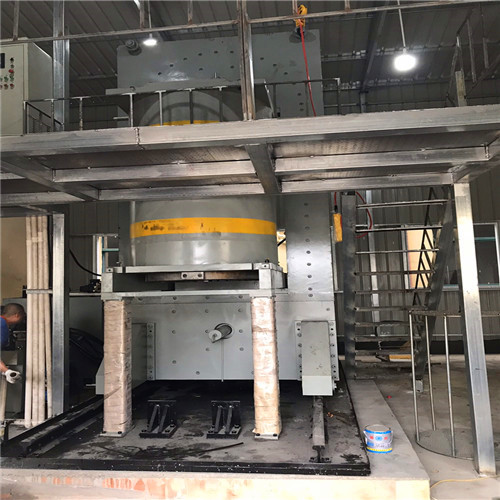
It is a molding method that utilizes the incompressibility of liquid media and uniformly transfers pressure.
The main differences between dry pressing and isostatic pressing are as follows:
Dry pressing for advanced ceramics
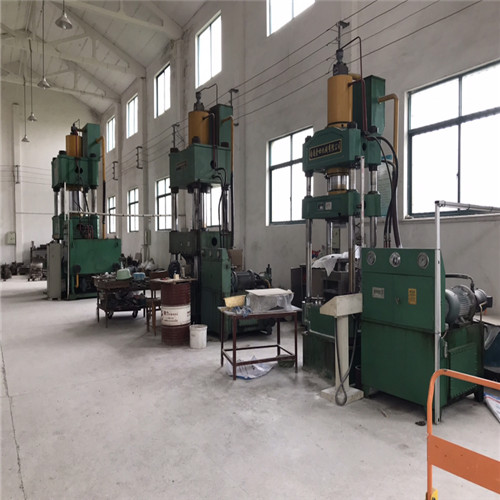
The dry pressing method is also called the dry pressing method, Its main features are as follows:The cost of dry pressing molds is high, and only mass production of the same product is economical and affordable.It is most suitable for parts that are not too large in geometric size, the long size is not too […]